Stay Integrated
The role of the digital twin in energy operations
Achieve operational excellence in the energy sector
By Joelle Beuzit
The digital twin: industry buzzword or valuable technological advance? While many industries acknowledge the value of the technology and gradually adopt it, the energy and utility industry has yet to reach digital maturity. Digital technologies permeate the sector more slowly than they do other industries. The digital twin is no exception: in 2020, less than 40% of oil and gas companies had implemented or planned to implement the technology.
On the other hand, the energy sector is under tremendous pressure to achieve superior efficiency across all its operations. Operational efficiency is a key driver for the adoption of digital technologies.
So, what roles can the digital twin play for the industry and what benefits does it bring?
The digital twin lifecycle To start with, a short recap: the digital twin is a virtual replica of a physical object, system, product, or facility, depending on the scale of the investigation. The digital twin is not a digital snapshot of a product at a certain point of its lifecycle. It follows the product lifecycle and lives across it, from the early days of conceptual design to manufacturing, operational use, and retirement.
In the capital-intensive energy sector, equipment and facilities remain active for 20 to 30 years or more. Preserving and extending the lifetime of expensive machinery and amenities translates to massive savings, while planned or unplanned downtimes may cost millions of dollars.
Particularly in this sector, the digital twin helps better analyze, understand, and eventually predict operational issues. It offers a critical advantage while possibly saving operational expenses. A predictive digital twin can help achieve operational excellence. Today, real-life examples reveal the value of the digital twin in the energy sector and demonstrate the role of predictive engineering analytics in enhancing efficiency.
The four levels of digital maturity of the energy and utility industry (Source: Strategy&)
Predictive data analytics for the digital twin What is the traditional process for ensuring a product or system's operational efficiency? It is a functional loop that starts with retrieving operational data from the sensors instrumented on the system. This data is captured and curated in one location. Using a dedicated software tool, the engineers perform data analytics and translate the retrieved information into actions: they now have sufficient evidence to make an informed decision. They can control, maintain or improve the system in operation.
Now, what if the system is so remote or intricate that it's nearly impossible to retrieve operational data? What if the engineers need to assess the impact of future or unexpected events on safety and integrity? What if they're trying to push the system beyond its current boundaries, under extreme environmental conditions, or beyond its expected lifetime? To answer these questions, engineers need more than measured data from sensors. They need predictive data. Predictive data combines the facts nested in the data with simulation to turn information into insights. It becomes available in places and times where measurements are impossible.
The digital twin is not about simulation alone. It relies on predictive engineering analytics, the application of multidisciplinary engineering simulation, coupled with intelligent reporting and data analytics.
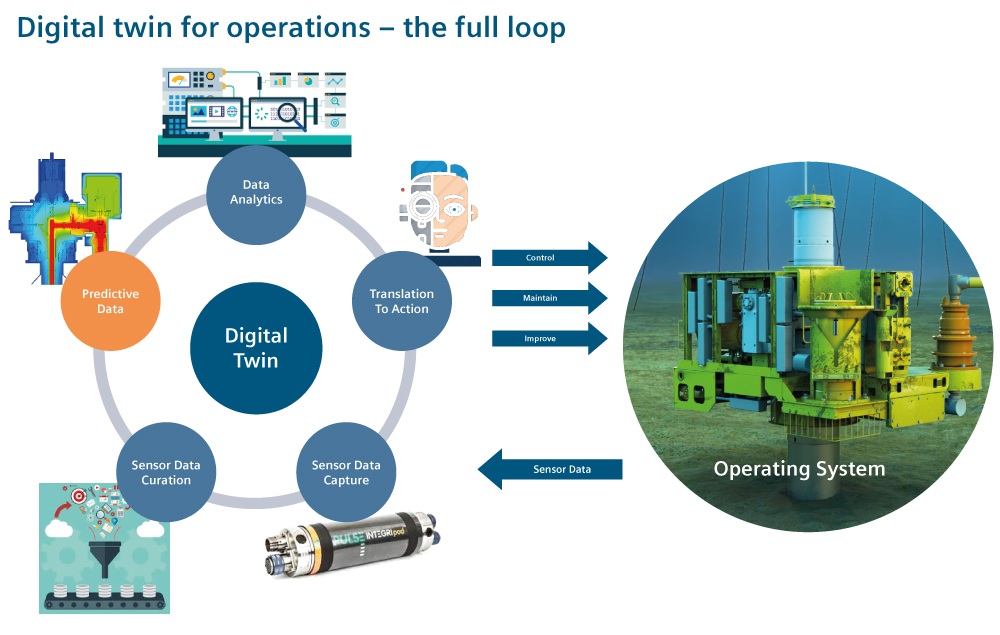
The digital twin in operations
Ensure the integrity of a heat exchanger Now, here comes the real-life example. Let us look at how the digital twin can support the operational integrity management of a heat exchanger. A heat exchanger is a system that transfers heat between two or more fluids. Heat exchangers are standard in many facilities and offer heating, refrigeration, air conditioning, cooling of power stations. They are part of many chemical and petrochemical plants, petroleum refineries, natural gas processing facilities, and water treatment systems. The systems typically consist of a tube bank and a plate; the steam goes into the bank of tubes and comes out again on the other side.
In this case, the heat exchanger displays a poor flow distribution into the tube bank. It generates high-temperature gradients with hot and cool spots. As a consequence, it induces thermal stresses, fatigue issues, and potentially cracking of the pipes. And therefore, it causes a potential integrity challenge.
How can the digital twin help address this challenge? Measuring the temperatures is the first step, but it won't yield insights into the system's future behavior. Accurately assessing and even forecasting the system's integrity would require additional information such as the stress history and the realistic remaining lifetime of the equipment. In short, it requires more insights from the temperature data. How do we retrieve these insights? There is no single method to undertake predictive engineering analytics. Modeling and simulation can take several forms, from the extensive 3D computational fluid dynamics and finite element analysis models to system simulation models or reduced-order models. Selecting the most appropriate technique depends on the simulation objective, the required details, and the acceptable time in which results are required.
To assess the heat exchanger's integrity, we can generate a model that comprises both high-fidelity finite element analysis and computational fluid dynamics. The model will help us understand and predict every detail of the flow distribution and heat transfer. But simulating these phenomena is a time-consuming activity. Additionally, it may be complex to integrate the operating history and the working life of the equipment. Is the high-fidelity approach too time-consuming? Can we combine it with reduced-order models and teach the reduced-order models how to generate data in real-time?
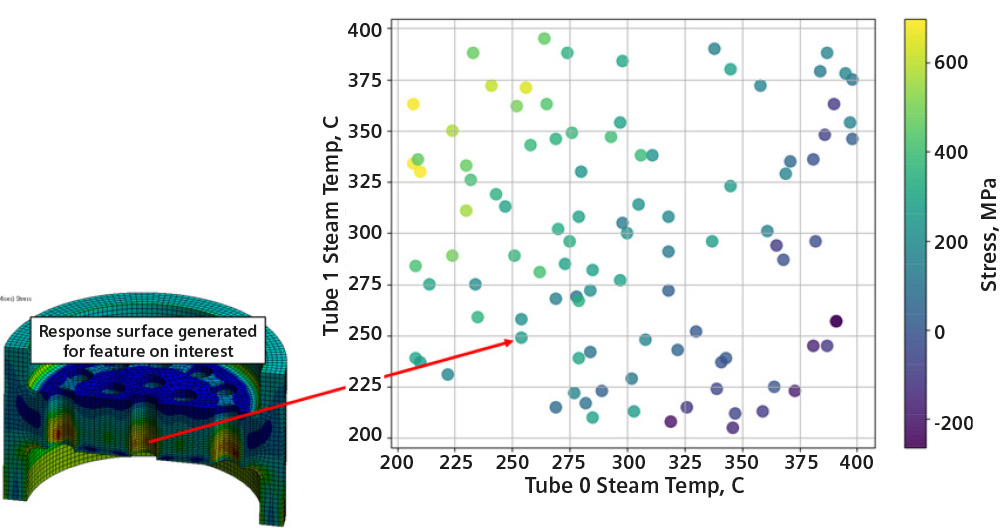
The correlation of the temperature and stress data at key locations of the steam tubes.
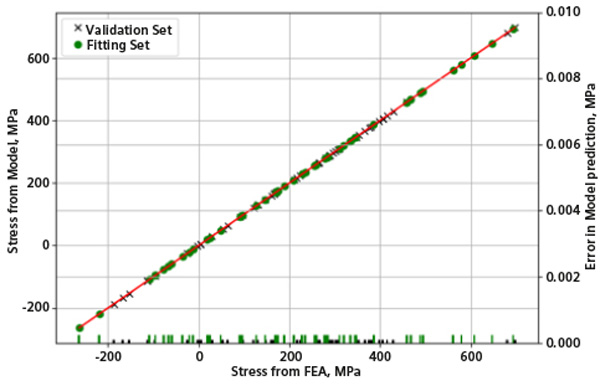
The correlation between the reduced-order model and the detailed stress predictions for one of the components in the heat exchanger
Define a process to predict integrity. The digital twin process starts with the same steps as the functional assessment loop. Sensors will measure the temperatures from the tube bank. The next step is to use a fluid dynamics simulation to understand the flow distribution in the tubes. Then, the engineers model the stress distribution within each tube where the heat transfer properties are known. They correlate it to the stress data using the finite element analysis model. In that way, they identify locations in the system which are critical to the system's performance. By characterizing the phenomenon across a set of scenarios, we can correlate the stress at different locations and the critical locations of the system with the temperatures we can measure. The final step is to generate a reduced-order model that engineers train to match the detailed predictive data.
The chart below (Figure 4) shows the correlation between the reduced-order model and the detailed stress predictions for one of the components in the heat exchanger. This correlation is beneficial to understand the effect of temperature-induced fatigue. Most importantly, the correlation is the starting point to build a reduced-order model that delivers a real-time assessment of stress and fatigue.
Application of the reduced-order model Now that the reduced-order model is fully functional, it drastically speeds up and enhances the operational assessment process. Again, it all starts with measuring the temperature inside the tubes. The measurement results in a time-series data stream from the tube bank. Inserting this data into the reduced-order model will automatically reveal the stress response. The reduced-order model-based fatigue analysis renders an updated fatigue life assessment. Based on this assessment, the engineers can inform operations: plan repairs, maintenance and downtimes, judge if lifetime extensions are appropriate. They have the operational temperature data at hand to create a real-life, real-time summary of the system's structural integrity. Predictive data helps them make informed decisions.
Data is essential The digital twin is a lifecycle notion. As engineers, we generate a tremendous amount of data in every step of the engineering process, from the initial concept through detailed design to the manufacturing and the operational life. This data should not be short-lived information. A meaningful usage of it will yield tremendous insights into the performance behavior of systems. It is essential that if we generate the data, we use it in operation.
For the energy and utility industry, it implies a change in how the supply chain works together. Operators take the equipment and put it through 25 years' worth of operation. In the near future, they'll have to work hand-in-hand with the equipment providers, who have the detailed technical and design knowledge of the products, and with the technology developers, who have the tools to create digital twins and the know-how to embed those into an operation. The digital transformation of the industry commands a closer collaboration of all involved throughout the engineering life cycle.
Which simulation method should you use in the predictive element of your digital twin? No technology prevails. Different simulation types play different roles in supporting concept, design, manufacturing, and operations, from high-fidelity models to system simulation and down to a reduced-order model. It depends on where you are in the lifecycle and what data you need. Predictive engineering analytics provides insights. In operations, it reveals its true value when coupled with field data. The example above highlights the immediate benefits of relying on a digital twin of a heat exchanger. But possibilities are endless, and applications of the technology range from integrity management to production performance and safety management.
Special thanks to Matt Straw (Norton Straw), Rikesh Mistry (Norton Straw), Ravi Aglave, Doug Kolak & Maged Ismail (Siemens Digital Industries Software)